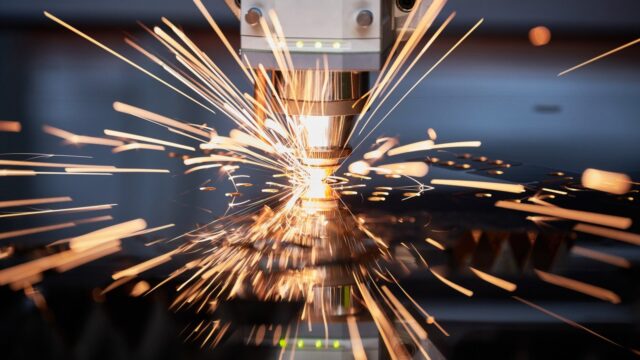
Precision cutting is essential in many industries, from manufacturing and construction to automotive and creative design. When accuracy and efficiency matter, metal laser cutting offers one of the best solutions for clen, precise cuts across various materials.
What Is Metal Laser Cutting?
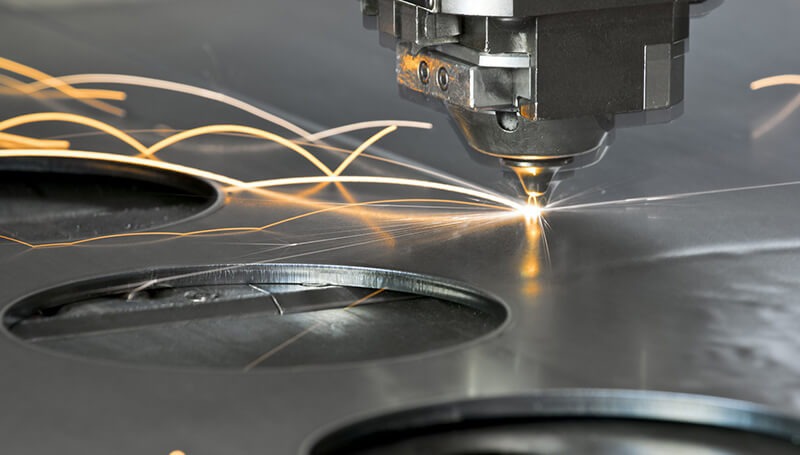
Metal laser cutting uses a high-powered laser beam to cut through metals with extreme precision. This method is preferred over traditional cutting techniques because it:
- Produces smooth, burr-free edges.
- Works on a variety of metals, including stainless steel, aluminum, and brass.
- Reduces material waste through highly accurate cuts.
- Supports complex and intricate designs that other methods struggle to achieve.
Choosing the Right Metal Laser Cutting Service
Finding a professional service that meets your needs is crucial. When searching for metal laser cutting near you, consider the following factors:
- Experience and Expertise – Companies with years of experience are more likely to deliver high-quality results.
- Material Capabilities – Ensure the service provider can work with the specific type of metal required for your project.
- Turnaround Time – Some projects require quick processing, so check for lead times and scheduling availability.
- Customisation Options – If you need unique cuts or engraving, look for services that offer custom solutions.
Industries That Benefit from Metal Laser Cutting
Manufacturing
Manufacturers rely on laser cutting for producing intricate parts with unmatched precision. The process ensures clean edges, minimal material waste, and high-speed production.
From small electronic components to large industrial machinery parts, laser cutting offers a consistent and efficient method for shaping metal.
Unlike traditional methods, it allows for complex geometries without requiring additional finishing, making it an essential part of modern manufacturing.
Automotive
The automotive sector depends on laser cutting to shape various components with extreme accuracy. Car parts and frames, exhaust systems, and intricate dashboard elements all benefit from this process.
Since laser cutting provides clean cuts without deforming the material, it is particularly useful for working with lightweight alloys and advanced metals used in modern vehicles.
This method also improves production efficiency, reduces waste, and supports the industry’s shift toward electric and hybrid vehicles by enabling the precise fabrication of battery components and specialized parts.
Architecture and Design
Architects and designers use laser cutting to create custom metalwork for both aesthetic and functional purposes. Decorative panels, intricate railings, signage, and even entire façades can be crafted with a high level of detail.
The ability to cut through various metals, including steel, aluminum, and brass, allows for limitless design possibilities. Whether for contemporary buildings or intricate restorations, laser cutting ensures that designs maintain their intended artistic and structural integrity.
Engineering
Engineering applications require components that meet strict specifications, and laser cutting provides the necessary precision for this purpose.
Engineers use laser cutting to produce prototypes quickly, allowing for faster design testing and refinement. The technology enables the fabrication of intricate and delicate parts used in aerospace, robotics, and advanced machinery.
Since laser cutting can handle different metals with varying thicknesses, it supports the development of innovative solutions in engineering, contributing to advancements in multiple fields.
Custom Laser Cutting for Unique Projects
Custom laser cutting allows businesses and individuals to create specialized metal designs tailored to their specific needs. Whether producing artistic installations, custom signage, or unique prototypes, laser cutting offers flexibility in:
- Complex Geometries – Create intricate shapes with high precision.
- Varied Thicknesses – Cut metals of different thicknesses without compromising quality.
- High Repeatability – Ensure consistency in mass production and custom projects alike.
How to Ensure Precision in Laser Cutting
Achieving precision in laser cutting depends on various factors. Ensuring the best results requires attention to:
- Proper Material Selection – Different metals react uniquely to laser cutting.
- Optimal Laser Settings – Power levels, speed, and focus need to be fine-tuned.
- Advanced Machinery – High-quality lasers provide cleaner, more precise cuts.
- Skilled Technicians – Experience plays a key role in achieving consistent results.
- Software Optimization – Using CAD software ensures accurate and repeatable designs.
Cost Factors That Impact Metal Laser Cutting Prices
Various elements affect the pricing of metal laser cutting, each contributing to the final cost of a project. From material properties to production scale, understanding these factors helps in budgeting effectively.
Material Type and Thickness Dictate Expenses
Different metals have varying levels of hardness, conductivity, and reflectivity, all of which influence laser efficiency.
Thicker materials demand higher laser power, increasing both energy consumption and operational costs.
More durable metals, such as stainless steel or titanium, often require specialized laser settings, further affecting pricing.
Design Complexity Adds to the Costs
The more detailed and intricate a design, the longer it takes to cut. Complex patterns require precise programming, often involving additional time for setup and adjustments.
Fine details, sharp angles, and elaborate engravings can increase the overall cost, especially if special software or multi-step processes are needed.
Batch Size Determines Per-Unit Pricing
Larger orders generally reduce the cost per unit because they maximize machine efficiency. When cutting in bulk, material utilization improves, and the setup time is distributed across multiple pieces.
On the other hand, smaller projects may result in higher per-unit costs due to wasted material and frequent machine recalibrations.
Finishing Requirements Influence Final Costs
Raw-cut metal may not always meet project specifications. Additional finishing processes like deburring, polishing, or protective coatings add extra steps, increasing both labor and material costs.
Some high-end finishes, such as anodizing or powder coating, further drive up expenses but are necessary for specific applications.
Machine Time and Setup Complexity Affect Overall Pricing
Every project requires machine calibration, file adjustments, and testing before the actual cut up begins. Longer setup times, especially for unique materials or unconventional shapes, lead to increased operational costs.
The more complex the configuration, the greater the labor involved, making setup a crucial pricing factor.
Environmental Benefits of Laser Cutting
Laser cutting is an energy-efficient alternative to traditional methods. Unlike mechanical cutting, it reduces material waste by using precision-focused beams.
Additionally, it does not require physical contact with the metal, eliminating the risk of wear and tear on cut up tools.
Beyond reducing waste, laser cutting limits pollution by avoiding the use of harsh chemicals or excess heat treatments.
Many industries are turning to this method for eco-friendly production solutions, particularly in sectors where sustainability is a priority.
Getting the Best Results
Working with a reputable metal laser cutting provider ensures that your project is completed accurately and efficiently. Whether you need industrial-grade cut up or a one-off custom design, choosing a trusted service with advanced equipment will deliver the best results.
By considering experience, capabilities, and turnaround times, you can find a provider that meets your specific needs while ensuring high-quality cuts and professional service.